Implementation of flow technology for continuous microencapsulation through emulsion based techniques
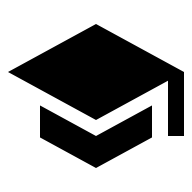
Category
Ph D Defense
Date
2020-11-04 09:00
Venue
KU Leuven, Campus Diepenbeek, Gebouw B, C102 - Aula 01.C102 - Agoralaan gebouw B, 3590 Diepenbeek
Hasselt, België
Hasselt, België
Promovendus/a: Sven Gobert
Promotor(en): Prof. dr. ir. Leen Thomassen, Prof. dr. ir. Simon Kuhn, Prof. dr. Leen Braeken
Microcapsules are spherical particles, consisting of a liquid core with an active ingredient, protected by a shell material. The shell determines how and when the active core is released to the environment. This way of controlling the release of active components has led to the development of an extensive range of new products within the pharmaceutical, food, textile, and construction industries. As a result, there is an increasing demand for large-scale production methods of microcapsules. A possible approach is to switch from conventional batch processes to continuous processes for the production of microcapsules. This doctoral research therefore focuses on applying flow technology for the production of microcapsules. Microcapsule formation is a two-step process. The first step is the formation of an emulsion by intensive mixing, while in the second step a shell is formed around the emulsion drops by a polymerization reaction. This emulsification and encapsulation were first studied separately for two emulsion-based microencapsulation processes: interfacial and in-situ polymerization. Then both optimized process steps were combined into a completely continuous system. Emulsion formation was investigated in a recirculation loop setup driven by a pump and static mixers or by an inline rotor stator mixer. Tubular reactors and a multi-stage continuously stirred tank reactor (MCSTR) with temperature gradient were examined for the encapsulation step. The results of the inline rotor stator mixer set-up showed that the feed flow rate from lab scale (200 ml/h) to production scale (20 l/h) could be increased without changing the capsule size distribution. This arrangement therefore prevents upscaling problems such as a change in geometry of the mixer. The encapsulation step was successfully performed in a tubular reactor for the interfacial polymerization and for the in-situ polymerization in the MCSTR. In addition, for the in-situ polymerization, the thermal stability of the emulsion was improved by aging the prepolymer. This shortened the total time required for encapsulation in the MCSTR by 50%. Capsule sizes for both encapsulation processes are around 10 µm with a production rate of 200 g per hour for interphase polymerization and 8.4 kg per hour for in-situ polymerization. This project demonstrates that emulsion-based micro-encapsulation can be successfully performed and scaled in a continuous reactor, if the emulsion is formed by a rotor-stator mixer in a recycle loop and the encapsulation reactor is tailored to the required process conditions determined by the chemical system.All Dates
- 2020-11-04 09:00
Powered by iCagenda